Chapter 3:
Managing crisis and ideas
Kessler LLC is a leading global automotive supplier operating in over 30 locations across four continents. Headquartered in the Midwest United States, Kessler's development capabilities include in-house design, rapid prototyping, testing resources, and R&D centers. They design three
product lines:
1. Closure systems
Elements like door and latch systems, strikers, and actuators that are used for door, mirror, and glove box movement.
2. Interior systems
Components for interiors like fabric, instrument panels, and consoles.
3. Motors and electronics
Functionalities like sunroof motors, window regulators, and seat
movement regulators.
Infrastructure
Kessler's infrastructure comprises four verticals: engineering, manufacturing, supply chain, and operations (IT, HR, etc). The data flow for processes moves across these verticals, meaning Kessler's help desk environment is not restricted to just IT.
4000 Users
200 Technicians
46 Regions
A quick look at Kessler's user stats
Kessler's IT policy is to reevaluate its existing IT solutions every four years to confirm if they meet current industry security standards. If they don't, Kessler shifts to new solutions, adapting itself to the latest industry standards. When it felt its service provider was no longer meeting expectations, Kessler decided to change to ManageEngine's
help desk solution.
Service catalog
With over 60 templates, Kessler's service catalog utilizes a group-based configuration across its functions. Rather than assigning individual users, ticket assignment, notifications, approvals, and escalations are sent to groups. The majority of approvals are also triggered to groups consisting of users and technicians.
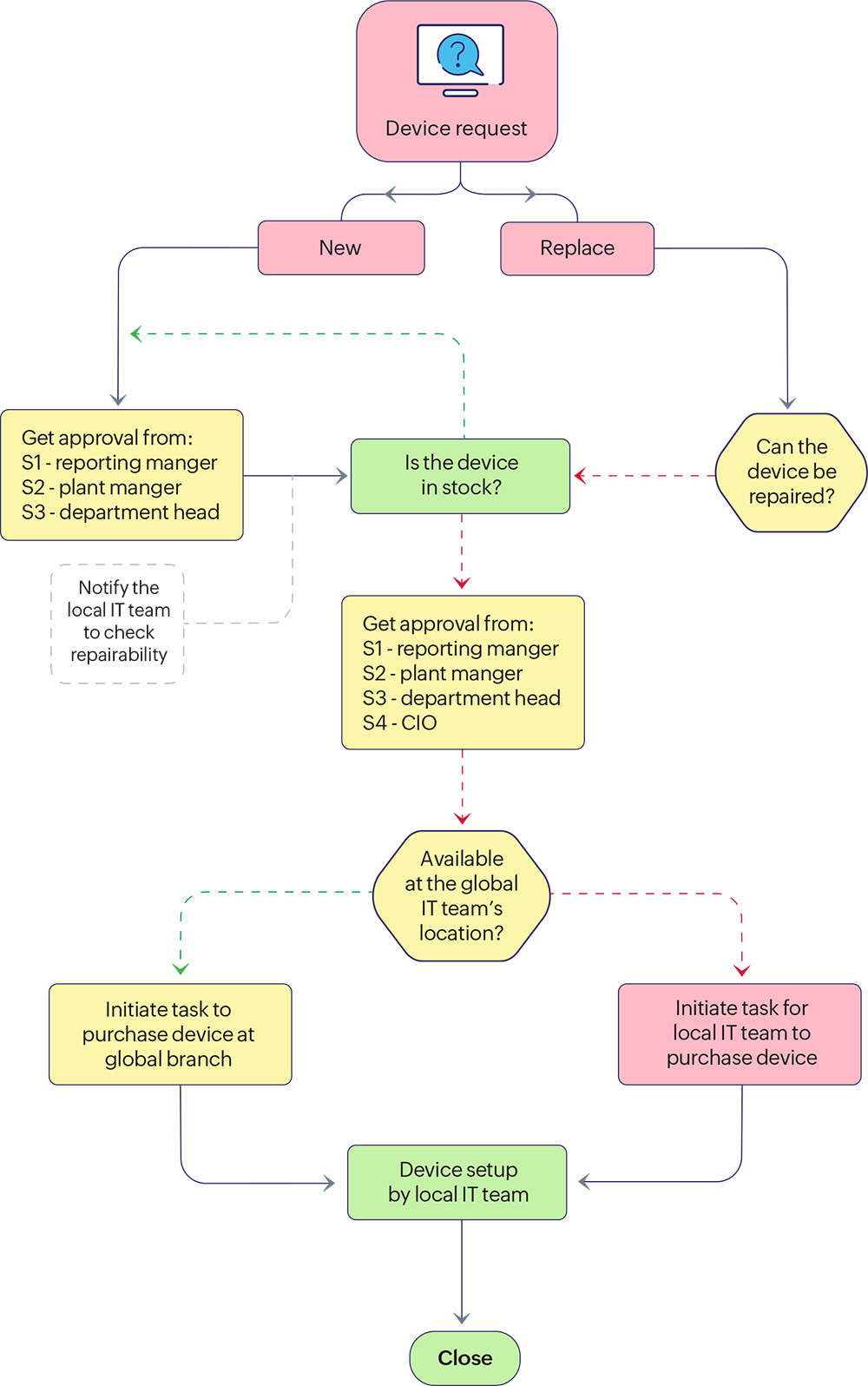
Crisis management
COVID-19 taught organizations the importance of crisis management and tested their resilience. However, the concept of crisis management is not new to the workplace. A crisis could be due to natural disasters, supply chain issues, challenges with personnel, or financial troubles, to name a few. IT plays a vital role in crisis preparedness. If operations are partially or completely affected, it is the organization's responsibility to engage the right teams to assess, take action, and resolve the crisis with minimal impact on business.
Incidents at Kessler are split into two categories: regular incidents and crisis calls. Since Kessler is a manufacturing company, they have multiple manufacturing plants. Shop floors don't have reliable internet access, so the incident management process relies on text messages to create incident tickets. The team opted for our help desk tool with an out-of-box connection with a third-party SMS service provider.
Each manufacturing site is set with an inbound number. When a user from that site sends a text message, an incident is created on the help desk. The ticket then gets assigned to the respective IT group at the local site. The group receives a text notifying them of the incident. They again receive an acknowledgment text, confirming the successful logging of the incident along with the ticket ID. These incidents can be logged from within any entity and are logged via the self-service portal or the mobile app.
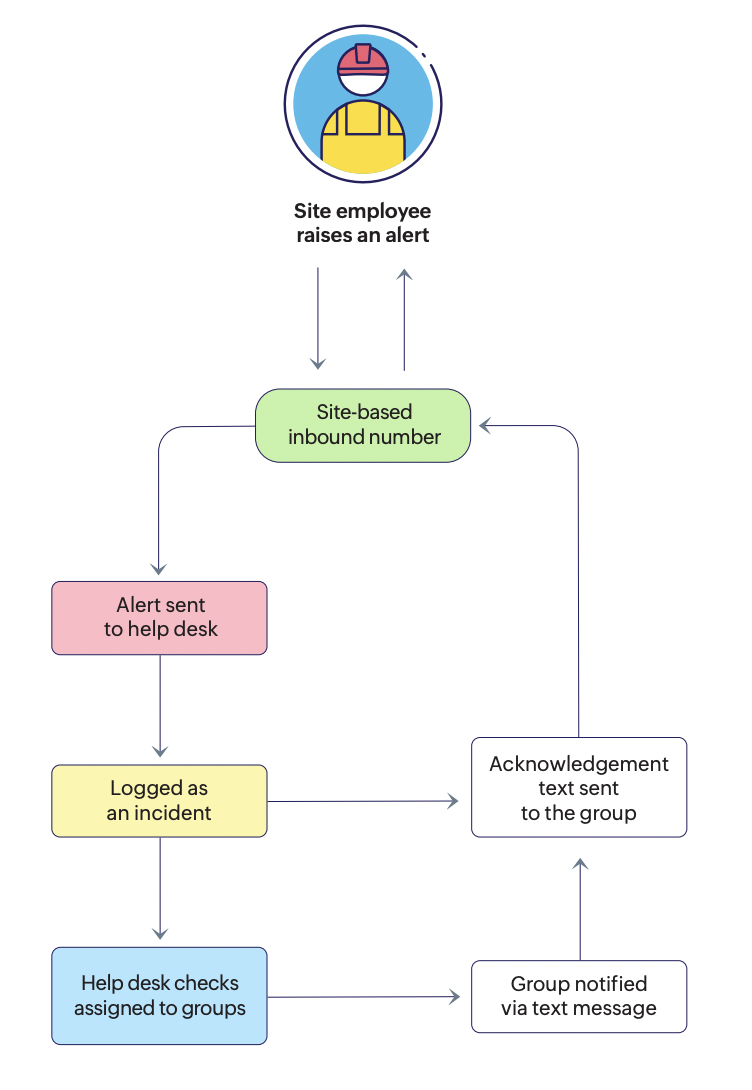
Incident notification workflow
When an incident escalates to an emergency, the plant employees can register a crisis call. Crisis calls are logged on three levels:
- Local or site level
- Regional or country level
- Global
For each level, there is a set of crisis groups that need to be notified on the crisis reported. These groups are maintained in a custom module on our help desk.
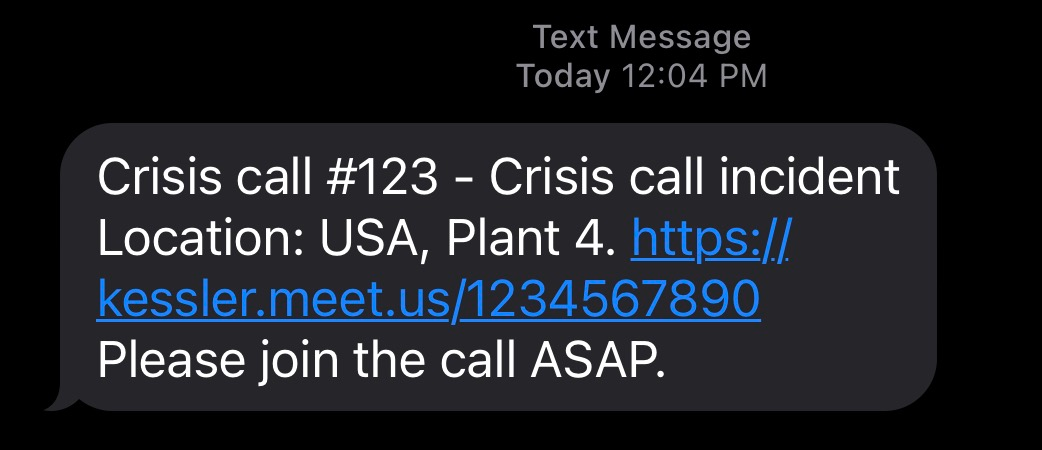
Sample crisis alert
When a crisis is logged, the system examines the level selected and the custom group associated with said level. It triggers an email and a text to the respective group members containing a meeting link corresponding
to the site.
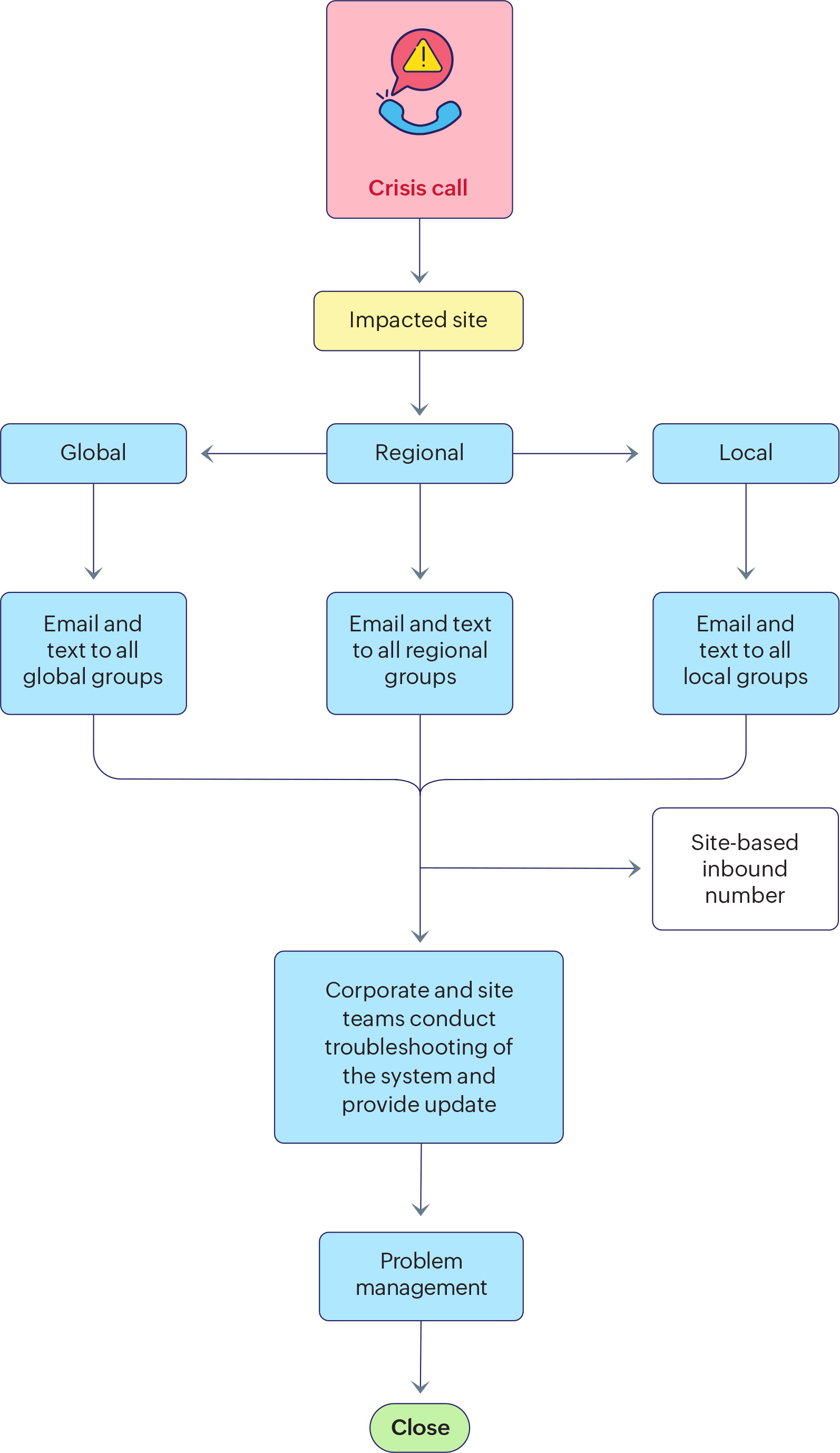
Crisis call workflow
Idea module
For a manufacturing process, or any process for that matter, to work efficiently, you need feedback at the grassroots level. In theory, your ground crew knows more about gaps and loopholes in real-life procedures than you. This is a concept Kessler understood early on and it made sure to incorporate feedback into its help desk with an Idea module.
When Kessler reached out to our implementation team with this requirement, this was not a feature we had on our roadmap. Nevertheless, we got to work and created a custom module interlinking the service requests, changes, and projects modules.
How does it work?
Let's say an employee believes the process chain would be further streamlined by repositioning the heating system. They can raise this as an idea ticket on the help desk. The idea is validated by the reporting manager and the site IT manager and passed on to the project management team for evaluation.
In this case, the idea submitted requires a relatively minimal investment of time, effort, and funds. So, the project management team moves the ticket forward as a change, i.e., a change to its existing process.
However, if the employee were to suggest a drastically different measure, like the introduction of new cooling equipment, this is categorized as a demand. A demand is a separate ticket that is once again sent to the second level of authorities for approval and then to the project management team for evaluation. If the equipment introduction can be carried out without disturbing the current chain of events, it is moved to the next phase as a change request. If it requires significant modification to the existing process, it is categorized as a new project.
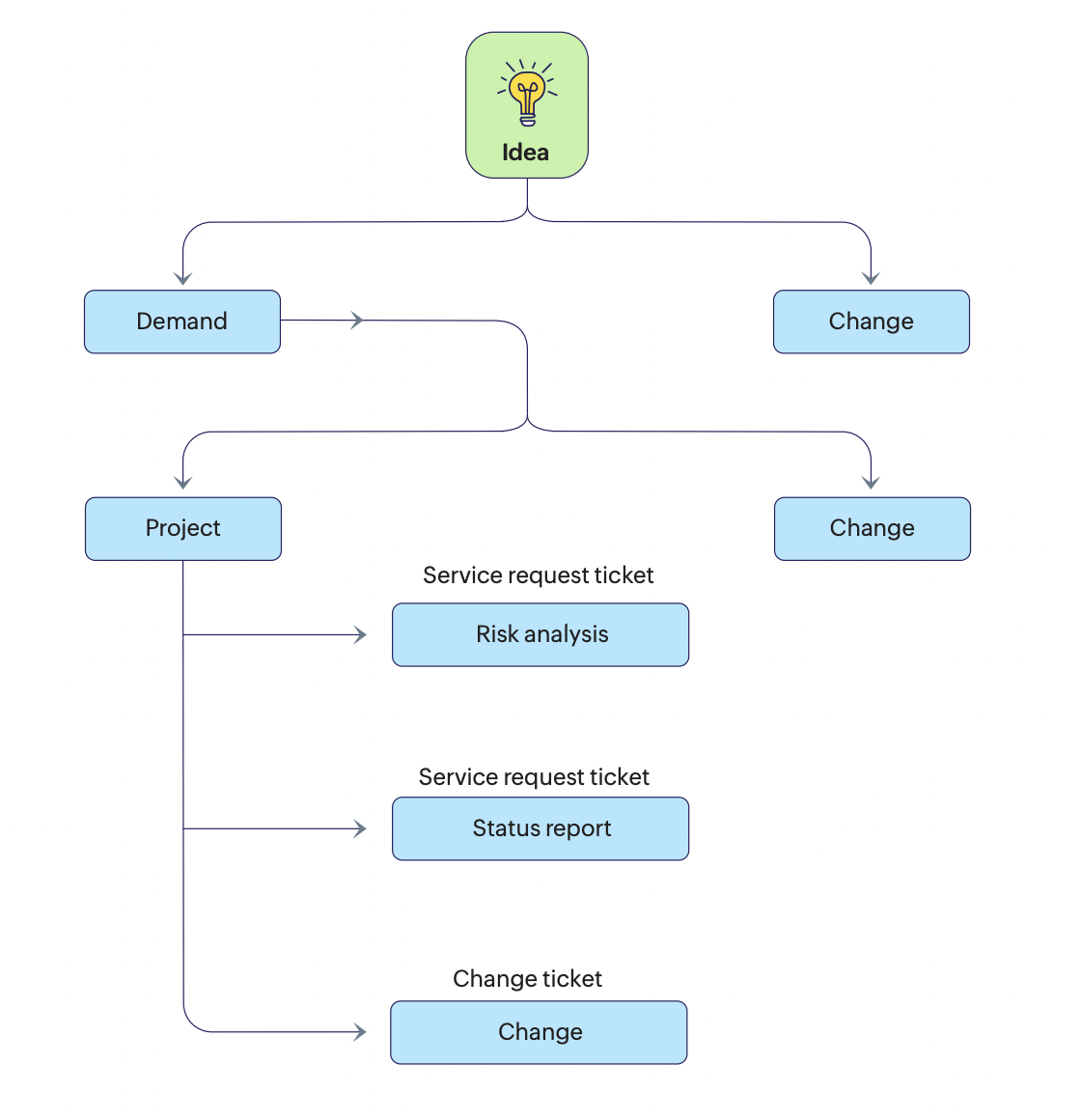
Once the demand gains approval as a project, the project management team is responsible for carrying out three sub-tasks: risk analysis, status report, and changes. When each sub-task is selected, a new ticket is created and associated with the project. For risk analysis and status reports, a service request is created, and for a change, a change ticket is created.
Here's the best part: After a successful project implementation, the team has to provide weekly status reports. Each week's status report can be raised as a new ticket under the same project, allowing the leaders at Kessler's headquarters to understand the overall trend at a glance. This works for risk analysis and changes as well, improving the decision-making abilities of the organization as a whole.
Change management
Kessler's change management process categorizes changes as
standard and emergency changes. Standard changes are preapproved and have predefined data sets to be filled whereas emergency changes bypass the approval stage and enable approval after the implementation stage. Let's take a closer look at the change management workflow with the help of a scenario.
Standard changes
Consider a scenario where Kessler's manufacturing plant in Ohio (United States) has been affected by a malfunctioning assembly line. Its production rate has dropped to 80%. Preliminary investigation reveals that the factory has three machines that need to be repaired or replaced for operations to resume at regular speed. How does Kessler move forward?
Date of incident: January 22, 2023
Supply requirement: 10,000 parts
Current production: 6,000 parts
Production deadline: April 30, 2023
Since Kessler has nearly three and a half months to the deadline, a temporary pause on production to replace the malfunctioning parts will not cause any delay in delivery. This is considered a standard change. The local technician captures the following details:
- Implementation plan
- Rollout plan
- Back-out plan
- Business justifications
- Risk and impact analysis
Once the details are submitted, it goes for internal approvals and an additional external approval (if necessary). The ticket is then assigned to the group that handles machinery. It is then the assigned group's responsibility to purchase or refurbish equipment, conduct primary testing, and give the go-ahead to operate at full capacity. If the process is successful, the ticket is closed.
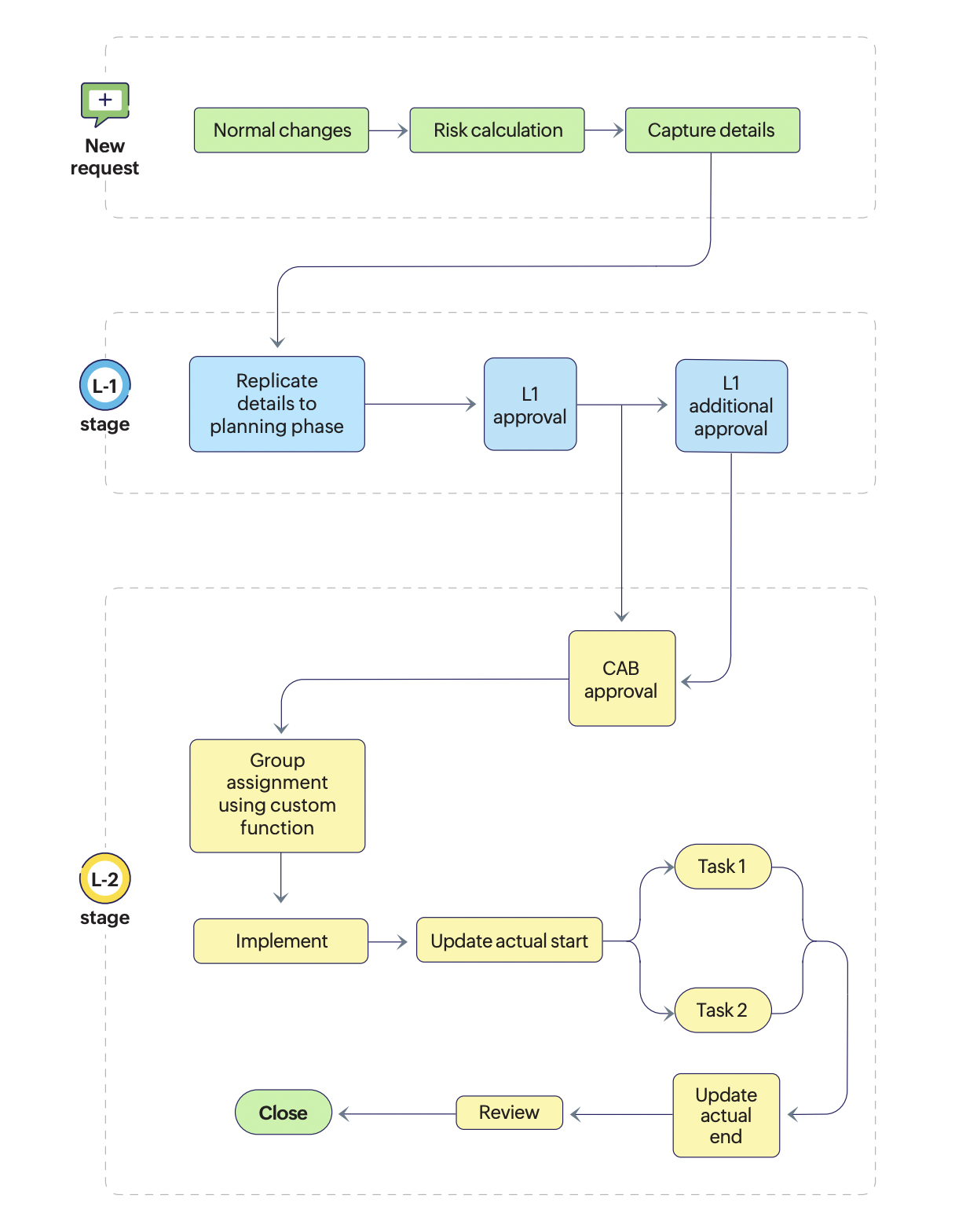
Workflow for standard changes
Emergency changes
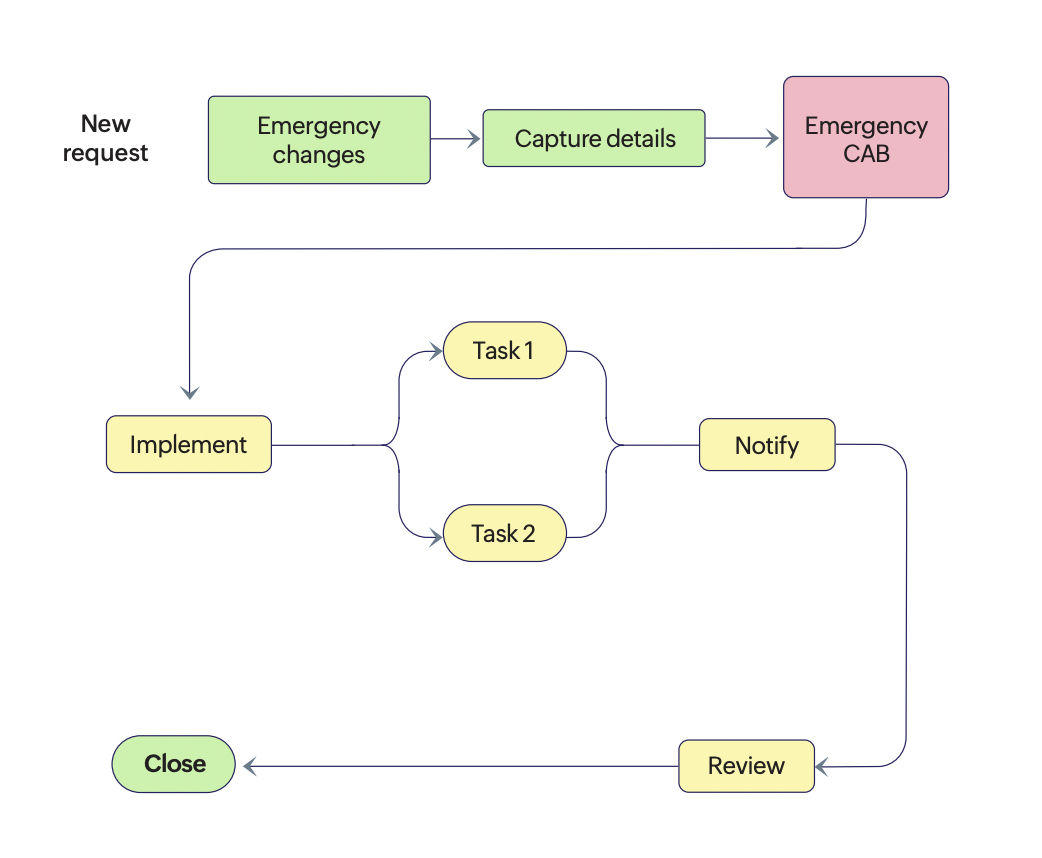
Workflow for emergency changes
In the same scenario, if the delivery deadline was at the end of January, it would be categorized as an emergency change. Here, the responsible groups cannot afford to wait for approvals as it would result in significant delays and ultimately, financial loss. Therefore, the manager for machinery and operations can go ahead with the implementation process, resolve the issue, and then send out a notification for analysis.