An ITSM guideline for manufacturing enterprises
We have seen the challenges, requirements, and the nature of ITSM for two different manufacturing enterprises: Cemm-Tech and Auto- Tech. While Cemm-Tech used our help to establish a system for all its employees, vendors, customers, etc., Auto-Tech did it predominantly for its employees in multiple locations. With any manufacturing enterprise, there are bound to be challenges simply because of their decades of experience using older systems. Many of the challenges we discussed earlier apply to smaller manufacturing companies, too.
If you are a manufacturer, it goes without saying that you own your process and your ITSM as well, like these two companies did. And you’re bound to face similar or different challenges. How you tackle them and make the right choices for your processes and needs will determine how successful your ITSM efforts will be. These two stories gave you an elaborate idea of how the two enterprises did that with ManageEngine’s assistance.
While you can take inspiration from these two stories, you need a guideline for yourself to help you tackle ITSM challenges in your own company. Your challenges are bound to be different, and this guideline will help you along the way.
Our experience with Cemm-Tech and Auto-Tech, and other manufacturing enterprises like them, has given us a fair idea of what ITSM should look like from a manufacturer’s perspective. To summarize it for you, we have the nuts and bolts of a manufacturer’s ITSM framework.
Nuts and bolts of a manufacturer’s ITSM framework
Service management guideline
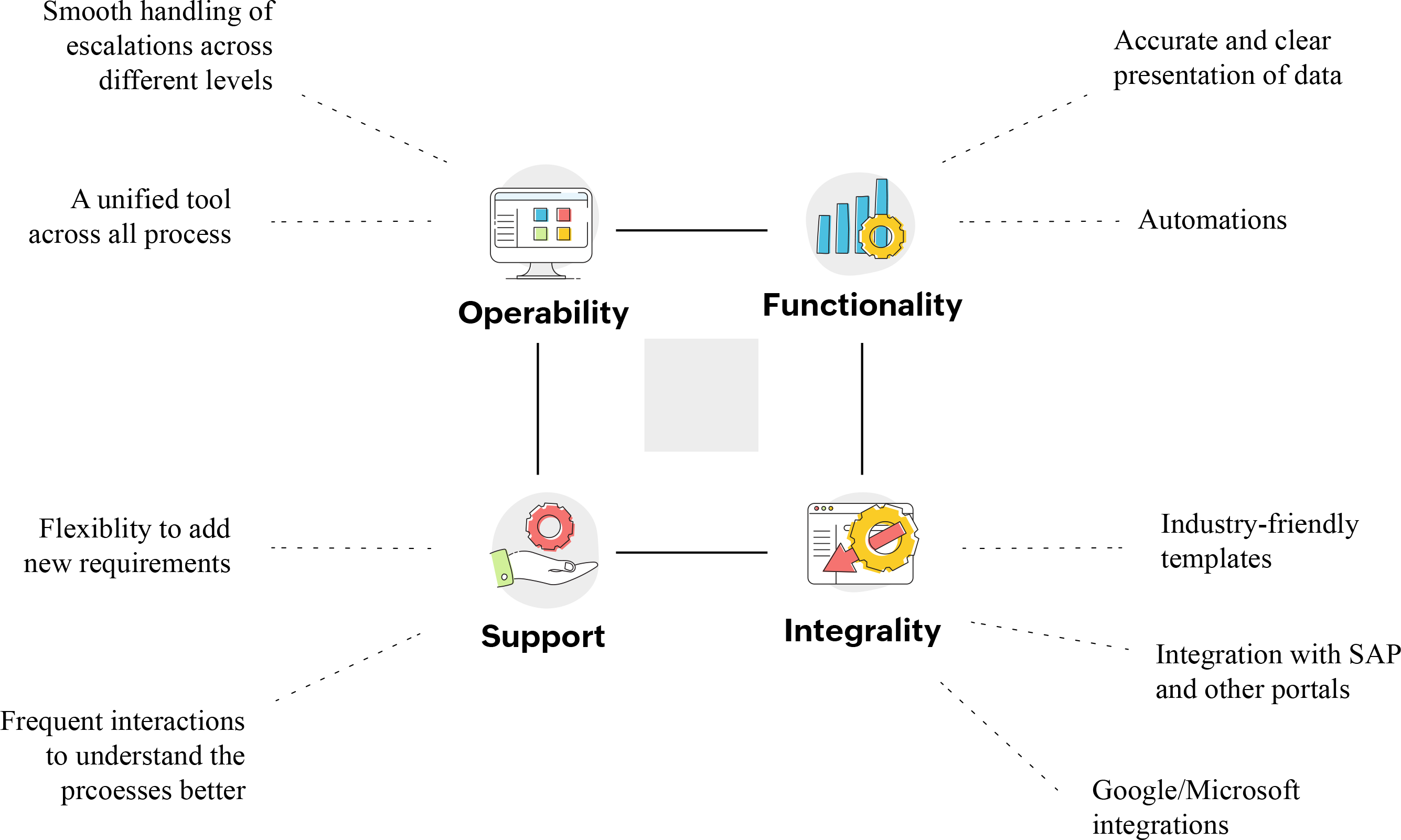
Support and tech
Cemm-Tech’s BSC 2 alone operates across 12 countries and needs the support of four languages. The company’s other business centers need even more. And beyond just language support, we interacted with both companies’ executives on a daily basis for months to understand their pain points and requirements beyond the surface level.
Auto-Tech’s complex set of requirements needed our support until the company’s IT team was capable of handling the ITSM tool by themselves.
You must be aware of the support you are going to get while implementing a solution. This includes:
- Support across languages
- Technical support to collaborate on new features
Conclusion
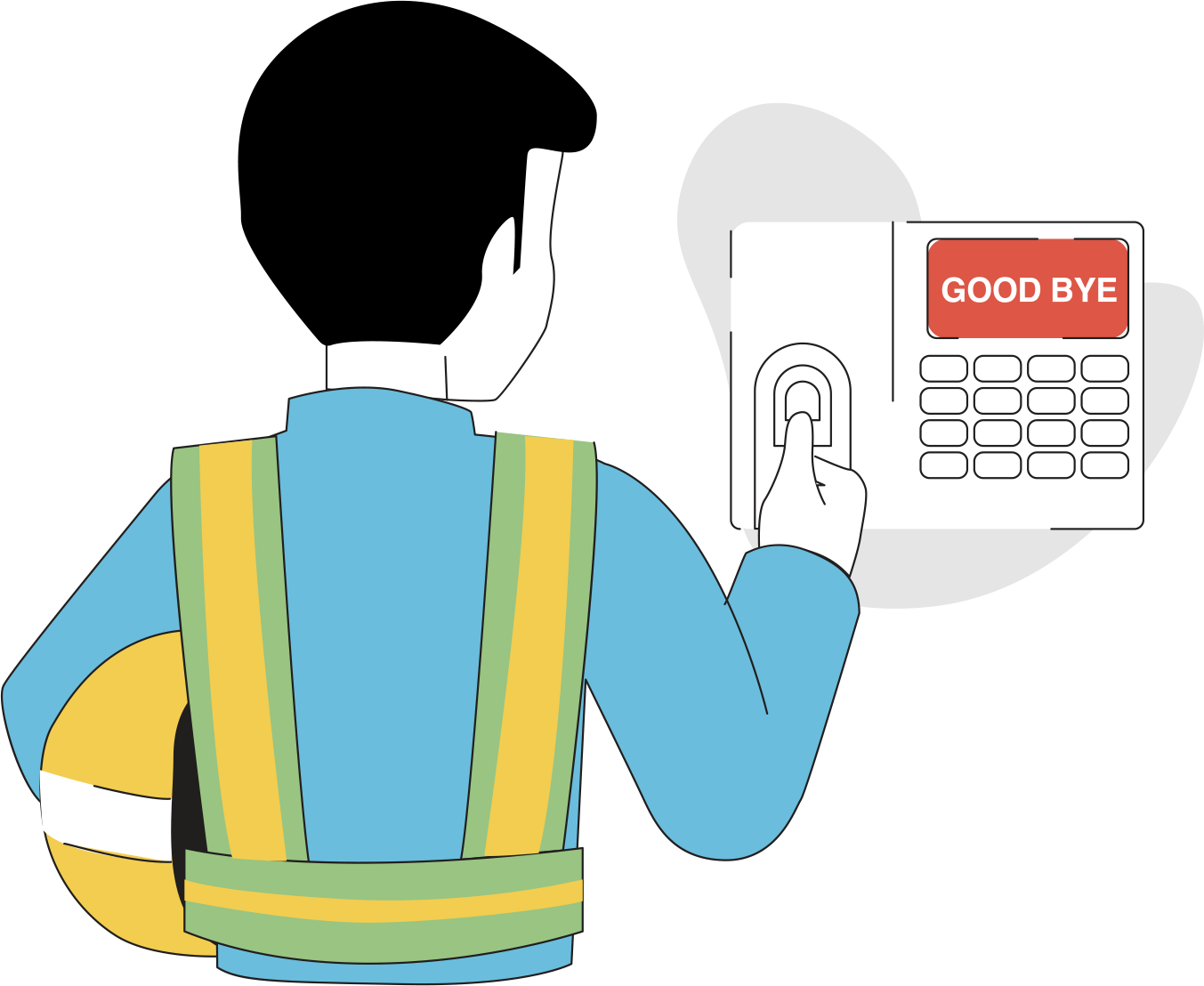
These guidelines are relevant for any manufacturer that operates like Cemm-Tech (like cement manufacturing, activated-carbon manufacturing, or bottle manufacturing) or Auto-Tech (automotive-parts manufacturing). These types of industries have their processes in the form of silos (process factories, as Cemm-Tech refers to them, or different departments, like Auto-Tech refers to them) and a team of IT people to handle requests from customers, vendors, and employees. For any such industry, implementing a comprehensive service management solution is a boost. And if you are in one such industry, these guidelines will help you.
The manufacturing industry is vast and has contributed to our learning over the years. It will continue to be one of the most interesting industries we work with. We learn from manufacturing companies’ requirements and our experience working with them, which helps us craft better ITSM solutions for the industry as a whole. Above all, we are delighted to help companies in the sector tackle challenges and improve their service management frameworks. We will share such interesting stories and guidelines in the future as we experience them.